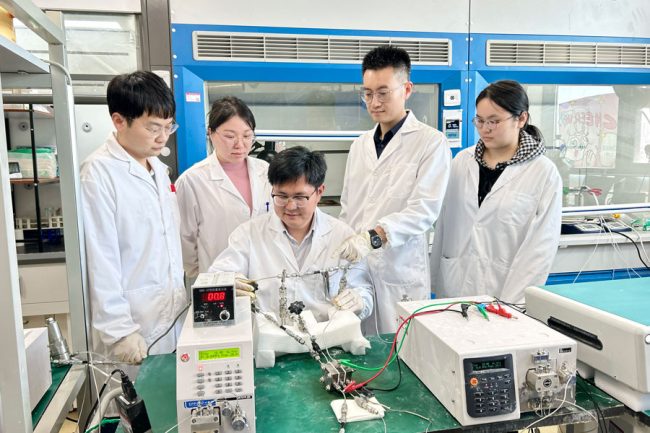
MAY 4, 2023 • By Tyler Irving
An international team of collaborators —including researchers from U of T Engineering and from Huazhong University of Science and Technology — has created a catalyst that efficiently transforms carbon monoxide derived from captured carbon into acetic acid.
By unlocking a new path to manufacture this key industrial chemical, which has a global market size of more than $10 billion per year, the innovation could spur new investments into carbon capture and storage.
“Carbon capture is feasible today from a technical point of view, but not yet from an economic point of view,” says Professor Ted Sargent (ECE), who recently joined the Department of Chemistry and the Department of Electrical and Computer Engineering at Northwestern University.
“By using electrochemistry to convert captured carbon into products with established markets, we provide new pathways to improving these economics, as well as a more sustainable source for the industrial chemicals that we still need.”
Sargent and his collaborators have a track record of using electrolyzers — devices in which electricity drives a desired chemical reaction forward — to convert captured carbon into key industrial chemicals, including ethylene and propylene.
In a paper published in Nature, they have now added acetic acid to the list.
Though acetic acid may be most familiar as the key component in household vinegar, recent graduate Dr. Josh Wicks (ECE PhD 2T3), one of the paper’s four co-lead authors, explains that this use accounts for only a small proportion of its global market.
“The acetic acid in vinegar often needs to come from biological sources, via fermentation, because it’s consumed by humans,” says Wicks.
“But about 90% of the acetic acid market is for use as a feedstock in the manufacture of paints, coatings, adhesives and other products. Production at this scale is primarily derived from methanol, which in turn is derived from fossil fuels.”
Wicks and the team consulted with life cycle assessment databases to show that for every kilogram of acetic acid produced from methanol, the process releases 1.6 kg of CO2.
Their alternative method takes place via a two-step process: captured gaseous CO2 is first passed through an electrolyzer, where it reacts with water and electrons to form carbon monoxide (CO). Gaseous CO is then passed through a second electrolyzer, where another catalyst transforms it into various molecules containing two or more carbon atoms.
“A major challenge that we face is selectivity,” says Wicks. “Most of the catalysts used for this second step facilitate multiple simultaneous reactions, which leads to a mix of different two-carbon products that can be hard to separate and purify. What we tried to do here was set up conditions that favour one product above all others.”
The team carried out detailed atomistic modelling to predict how changing the composition of the catalyst would influence which products were formed. They also looked at the impact of other factors, such as the pressure at which the reaction takes place.
Their analysis showed that using a much lower proportion of copper (approximately 1%) compared with previous catalysts would favour the production of acetic acid. It also showed that elevating the pressure to 10 atmospheres would be beneficial.
“Using room temperature and one atmosphere of pressure is a major advantage of electrochemistry compared to industrial thermochemical processes. However, we found that by increasing the pressure just a little bit in combination with electrochemistry — 10 atmospheres isn’t a big step compared to some industrial processes, which can be in the 60-100 atm range — we could achieve record-breaking selectivity.”
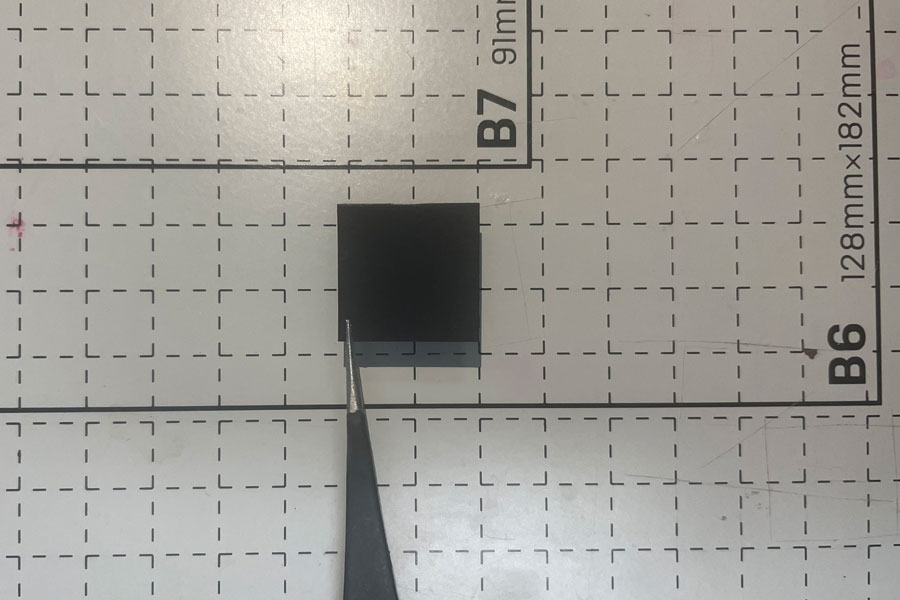
Based on the modelling, team members at Huazhong University of Science and Technology built a functioning prototype of the catalyst, which they tested in an electrolyzer. In the paper, they report a faradic efficiency of 91%, meaning that 91 out of every 100 electrons pumped into the electrolyzers end up in the desired product, in this case, acetic acid.
“That’s the highest faradic efficiency for any multi-carbon product at a scalable current density we’ve seen reported,” says Wicks. “For example, catalysts targeting ethylene typically max out around 70% to 80%, so we’re significantly higher than that.”
The new catalyst also appears to be relatively stable: while the faradic efficiency of some catalysts tends to degrade over time, the team showed that it remained at a high level of 85% even after 820 hours of operation.
Wicks hopes that the elements that led to the team’s success — including a novel target product, a slightly increased reaction pressure and a lower proportion of copper in the catalyst — inspire other teams to think outside the box.
“Some of these approaches go against the conventional wisdom in this field, but we showed that they can work really well,” he says.
“At some point, we’re going to have to decarbonize all the elements of chemical industry, so the more different pathways we have to useful products, whether it’s ethanol, propylene or acetic acid, the better.”
“Sustainability solutions are as much about asking the right questions and challenging the way things have always been done,” says Professor Deepa Kundur, Chair of ECE. "By exploring new paths and by positioning carbon capture as an attractive option from an economic perspective, the Sargent Lab team is giving it every chance of catching hold."
Story from U of T Engineering News, with files from Matthew Tierney